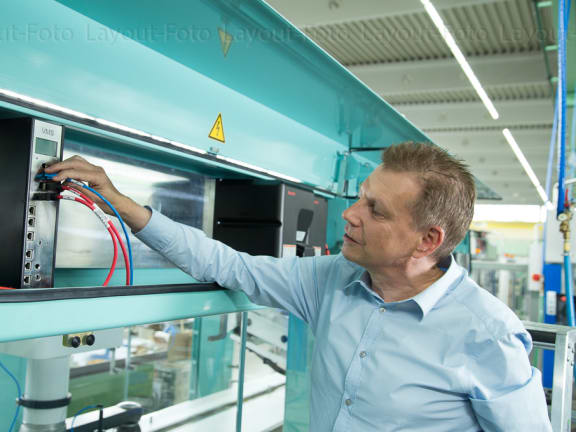
The tool control mounted on a robot is directly connected to the VMS packaging machine control (on this image).
Clear error messages
One VMS module is responsible for controlling the functions of each sub-machine. Robots with their tools, Transmoduls, NC axes, frequency converters, actuating drives, scanners, cameras, user guidance, error visualisation, PLC functionality, the integration of third-party devices and the connection to higher-level software systems are all integrated with the packaging machine control system – via a single software. Via IO-Link, it is now possible to not only transmit digital switching information from and to VMS control, but to also make available further phases of a sensor/actuator. “With the WK5, we are bridging the IO-based, modern bus systems and a physically straightforward IO signal. This enables error messages to be clearly assigned,” says Tobias Ott, Head of Embedded Software at Schubert System Elektronik. The WK5 is designed such that every IO-Link-enabled component can be controlled. The new control technology opens the door for the development of further applications for Schubert’s robot tools. And, over the next few years, it will entail further innovations in the field of automated packaging applications.
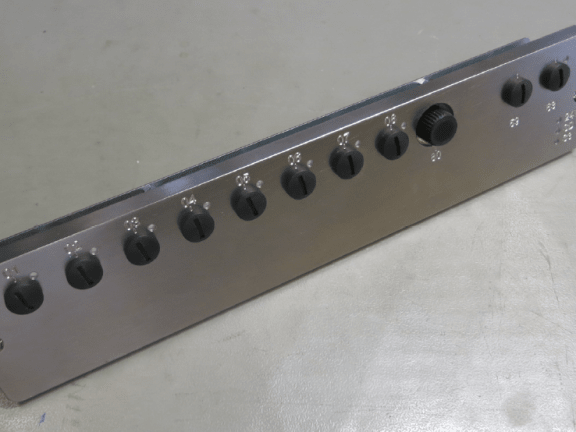
The tool control WK5 has been developed by Schubert System Elektronik (SSE), a subsidiary of Gerhard Schubert GmbH Verpackungsmaschinen.
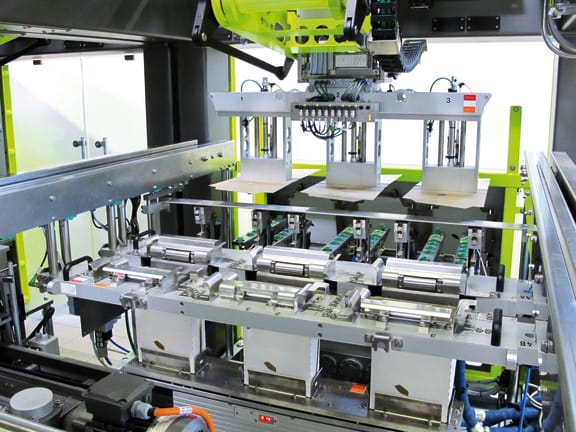
In this case, the WK5 is mounted on a F2 packaging robot.