A high-profile flagship for a sustainable future
Although the actual construction of the final assembly hall and office building began in spring 2022, the L2218 road between Crailsheim and Dinkelsbühl had to be relocated three years earlier to create space for the new buildings. Now, with their lofty, streamlined design, they blend seamlessly into the overall complex. A total area of 13,000 square metres was created, of which the assembly hall alone takes up 8,500 square metres. Totalling 45 million euros, the project represents the largest single investment in the company’s history and strengthens Schubert for the future in three key respects. Firstly, the area for final assembly will be increased by 30 per cent, which will enable greater production capacities and therefore further growth for the company. Secondly, attractive premises are being created for 300 new workspaces, tailored to meet the needs of tomorrow’s working environments. And thirdly, the new buildings will be entirely climate-neutral thanks to an ingenious energy concept.
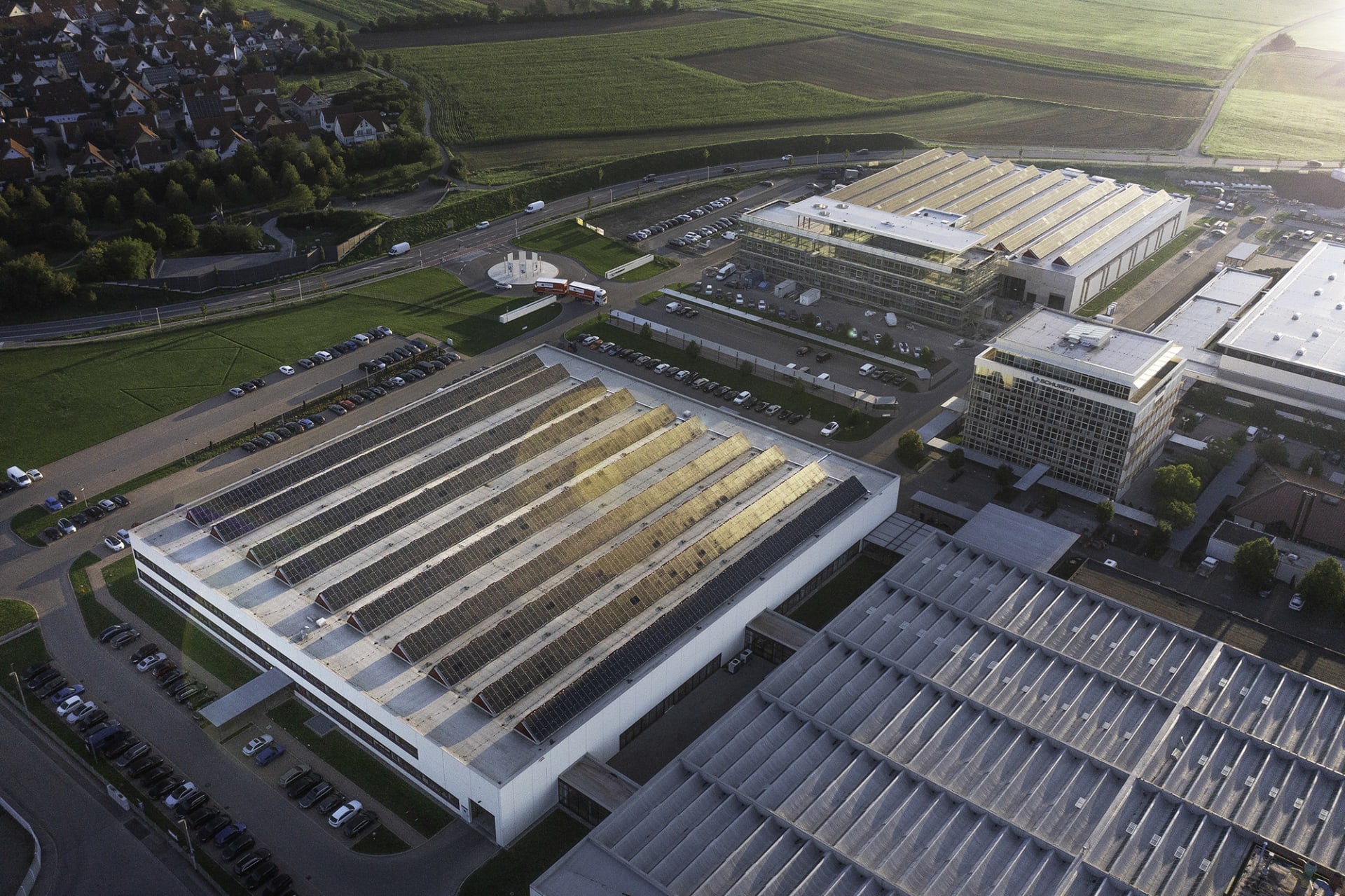
Schubert covers a quarter of its electricity requirements with the photovoltaic system on the roof of the new final assembly hall and on a neighbouring hall.
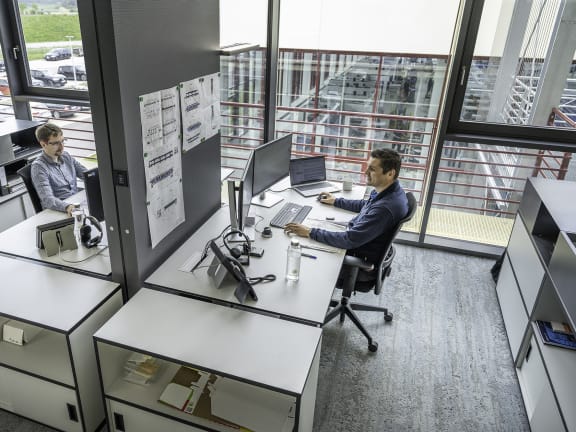
The new buildings bring design and assembly even closer together, as the direct view into the assembly hall reveals.
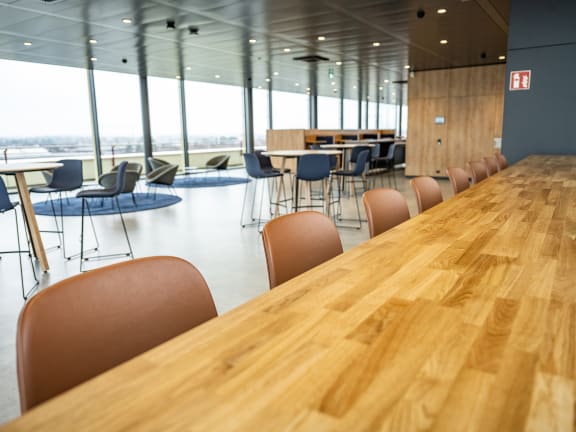
Attractive meeting points and work areas have been created throughout the building to encourage exchange and dialogue.
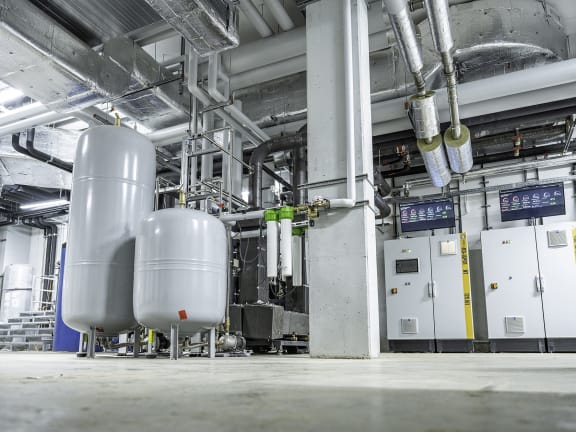
State-of-the-art control technology guarantees efficient operation of the heating and cooling centres as well as optimum energy distribution.
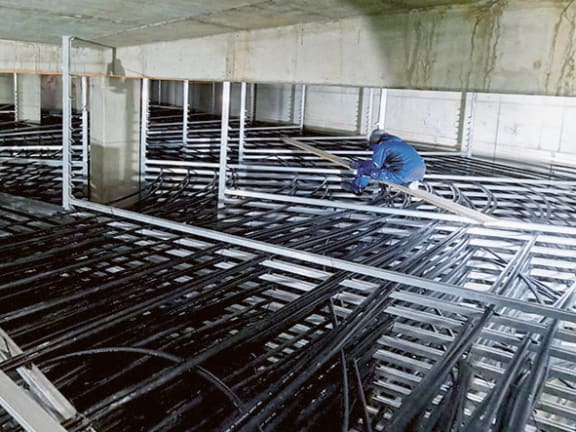
The ice storage under the hall is one of the largest of its kind in the world, with a reservoir of 1.9 million litres of water.
Ice storage as a key element
The functional principle is quite simple: When heat is extracted from water, it freezes into ice, generating additional energy. This energy is harnessed for the building's heating circuit via heat pumps – until all the water is frozen. For the cooling function, the block of ice is simply defrosted again in the summer with the help of added heat.All useful waste heat has also been integrated into the overall concept. At the heart of the system, state-of-the-art control technology guarantees efficient operation of the heating and cooling centres as well as optimum energy distribution. Furthermore, the photovoltaic system on the roof of the new final assembly hall and a neighbouring hall provides more than one megawatt of self-generated electricity per year, which Schubert can use to cover a quarter of its requirements.
Gerald Schubert, Shareholder of the Schubert Group, is extremely pleased with the result: “With our Mission Blue Sustainability Initiative, we have set ourselves very ambitious environmental protection targets. We are delighted that we have now come a step closer to achieving them with these two energy-efficient new buildings.”