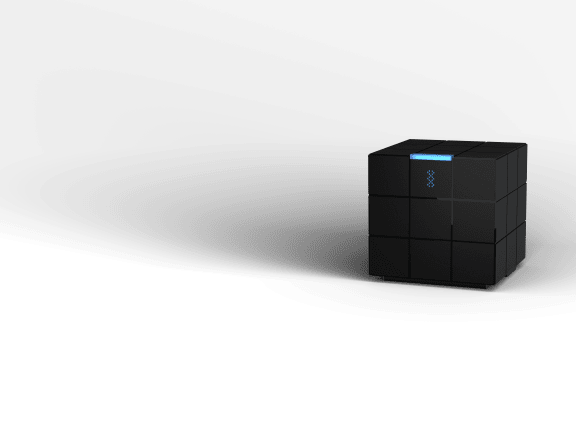
Schubert Additive Solutions developed an entirely new 3D printer for its customers.
Better packaging quality, short time-to-market
“Many products from the consumer goods sector are difficult to package due to their shape. Conventional grippers in packaging machines are not always ideally matched to the goods and they may drop products during the packaging process,” explains Conrad Zanzinger. But things are different when the tools are perfectly matched to the food or cosmetic product thanks to 3D printing. Not only does the process in the machine run more reliably, but there is also less waste because the products are placed safely into the packaging and do not slip out of the tool’s grip. Another advantage that 3D printing offers to FMCG (fast moving consumer goods) manufacturers is the tremendous flexibility that allows for a short time-to-market. As new products are added to the range, manufacturing companies can print their own format parts – without having to wait until the required tools are manufactured and delivered by an external company. This is especially important in the B2C industries, as new products are constantly being developed and launched throughout the year. Even seasonal products at Easter, in the summer or at Christmas time are no longer a problem when it comes to packaging: Quick tool changes, ideally matched to the product thanks to 3D printing, also speed up production.
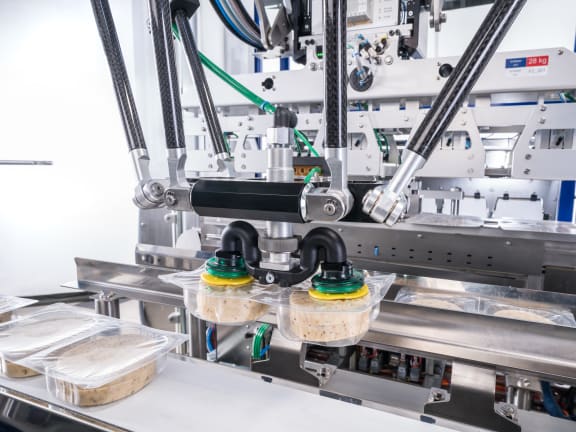
At Heinrichsthaler, the organic shape of the vacuum cups ensures a perfect grip on the soft plastic packaging of its Grilltaler barbecue cheese rounds.

Pastry manufacturer Bijou packages its madeleines and other sweet baked goods safely into a variety of unusually-shaped tins thanks to the 3D robotic tools.
Consistently high print quality
It was important for the developers at Schubert Additive Solutions to design a very simple solution for the new PARTBOX printer that could be used by anyone without much previous know-how. “By doing so, we are making the advantages of additive manufacturing accessible to everyone,” adds Conrad Zanzinger. If the customer owns a Schubert machine, he can call up the print jobs for the corresponding parts on the PARTBOX streaming platform. If new products need to be processed on the machine, Schubert develops suitable format parts and then uploads the print job to PARTBOX. “This allows the customer to easily print the required part in-house with the printer we developed,” says Conrad Zanzinger. The PARTBOX printer offers a consistently high print quality, which significantly improves process reliability within the packaging machines and therefore efficiency in the packaging process for customers. The use of high-precision components such as a milled aluminium frame, ball screws and a unique guiding technique ensures that the print head is positioned accurately. Schubert ensures the exact dosage of the printing filament by means of an extruder with direct extrusion. A ‘hood’ over the unit eliminates environmental influences such as heat or dirt.
The PARTBOX from Schubert Additive Solutions can be used universally, so not only parts for Schubert packaging machines can be produced, but also those from other machine manufacturers, as well as parts designed in-house. “Our streaming platform and the printer guarantee consumer goods producers the most rapid availability throughout the entire process. To produce tools, they do not need an individual printer for each production stage. With PARTBOX, they are very well taken care of,” explains Conrad Zanzinger. “At the same time, our customers benefit from high-level data security and easy operation.”
Partbox black plastic – food-grade and safe
Of course, all parts that come into contact with food, confectionery or cosmetics have to be certified accordingly. Especially for the production of spare parts – i.e. everything that comes into contact with products during the packaging process – it is important that the plastic material is wear-resistant. With PARTBOX Black plastic, Schubert Additive Solutions supplies the right printing material for the 3D printed parts. The difference versus commercially available filaments lies in a polyamide optimised for the FDM (Fused Deposition Modelling) printing process. The material is food-grade and detectable with a metal detector. PARTBOX Black also features excellent mechanical properties and high temperature resistance. This allows very smooth surfaces to be achieved in the printing process.
With its own streaming platform and printer, Schubert’s PARTBOX is now a complete system that also enables FMCG manufacturers to produce components with the fastest possible availability directly in their own operations – and with a high level of data security during the transfer and use of 3D data. Thanks to the digital process, customers save on process, shipping and warehousing costs and can compete more successfully in the market.