Alternative materials, smaller packaging sizes, innovative packaging concepts
Be it consumer wishes or legal regulations – the issue of sustainability is playing an important role for more and more food manufacturers. Gerhard Schubert GmbH, a packaging specialist who is very much aware of its responsibility, has always placed great importance on environmental awareness. The company has clearly defined extensive goals and measures with its Mission Blue Sustainability Initiative. In order to provide companies with the best possible advice on tackling this multi-faceted challenge, Schubert experts provide support with its Packaging Perspectives services in the selection of materials and the design of packaging solutions that are both machine-compatible and environmentally friendly.
Schubert’s flexible, modular and easily converted packaging machines process both conventional and fully recyclable packaging. Robot-based TLM technology handles a wide range of carton formats, trays, plastic crates as well as standard and paper-based flowpack films without compromising on quality. Martin Sauter, Head of Sales at Schubert, adds: “We are continuously developing our innovative packaging machines, especially in terms of sustainability. Last year, for example, we equipped our Flowpacker with Box Motion sealing technology, which enables cross-sealing using ultrasound. The seal is also ideal for recyclable flowpacks made from monofilms or paper-based films."
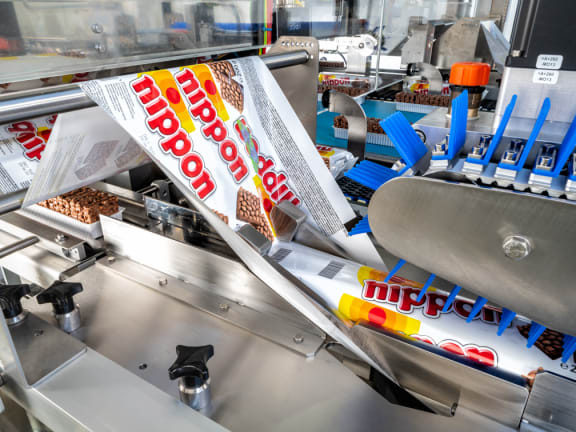
Schubert is also continuously developing the Flowpacker. Last year the Flowpacker was equipped with Box Motion sealing technology, which enables cross-sealing using ultrasound. The seal is also ideal for recyclable flowpacks made from monofilms or paper-based films.
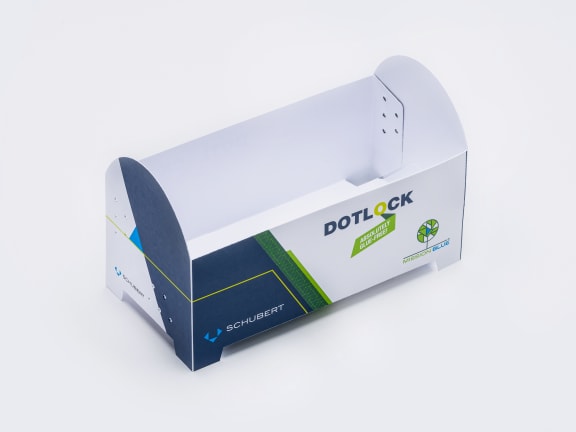
Dotlock is a 100 per cent glue-free technology for cardboard packaging that Schubert developed in-house.
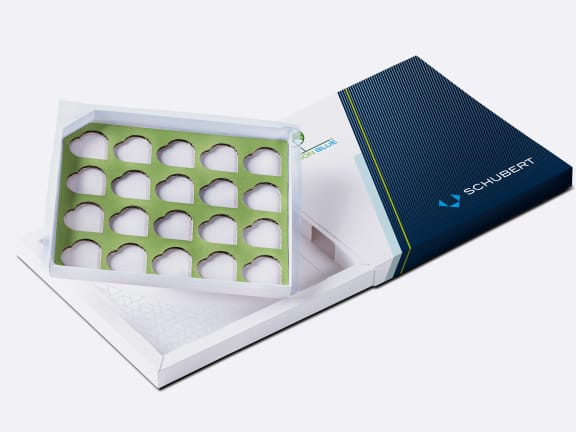
Among other innovations, the Schubert experts from Packaging Perspectives will be presenting a cardboard-monofilm hybrid solution without glue that significantly minimises the use of plastic.