Hauptsächlich zwei Arten von Siegelung bestimmen bisher den Markt für Schlauchbeutelverpackungen – das Kaltsiegeln und das konventionelle Heißsiegeln. Die häufig verwendeten Kaltsiegelfolien sind meist auf ein ganz bestimmtes Produkt zugeschnitten und entsprechend bedruckt. Das Material wird nur an den vorgesehenen Klebestellen mit einem latexbasierten Klebstoff beschichtet. Zum Verschließen der Siegelnaht presst die Siegeleinheit die Klebestellen mit Druck aufeinander. Da die Siegelung ausschließlich über den separat aufgetragenen Klebstoff gelöst wird, benötigt das Folienmaterial keine Siegelschicht. Die Siegelung ohne Hitzeeinwirkung prädestiniert die Kaltsiegelfolien für das Verpacken von wärmeempfindlichen Produkten wie Schokoladenriegel und ähnliches.
Kaltsiegelfolien sind in der Verarbeitung sehr einfach. Denn im Gegensatz zum konventionellen Heißsiegeln spielt die Zeit beim Verarbeiten von Kaltsiegelfolien kaum eine Rolle. Daher kann mit hohen Foliengeschwindigkeiten von 60 Metern pro Minute oder mehr verpackt werden. Dennoch weisen Kaltsiegelfolien einige Nachteile für Hersteller und Konsumenten auf: Sie sind etwas teurer als Heißsiegelfolien und aufgrund des Klebstoffanteils nur bedingt lagerfähig. Selbst bei optimaler Lagerung ohne Temperaturschwankungen und UV-Strahlung altert das Material und lässt sich dann nicht mehr einwandfrei siegeln. Für Konsumenten, die gegen Latex allergisch sind, kann der Latexanteil im Klebstoff ein Problem darstellen. Zudem bilden sich beim Öffnen der Klebestelle eines kaltgesiegelten Schlauchbeutels Fäden. Eine Schlauchbeutelmaschine, die ausschließlich kaltsiegeln kann, lässt sich nicht oder nur mit großem Aufwand auf ein Heißsiegelsystem umrüsten, bietet also keine Flexibilität beim Siegelsystem.
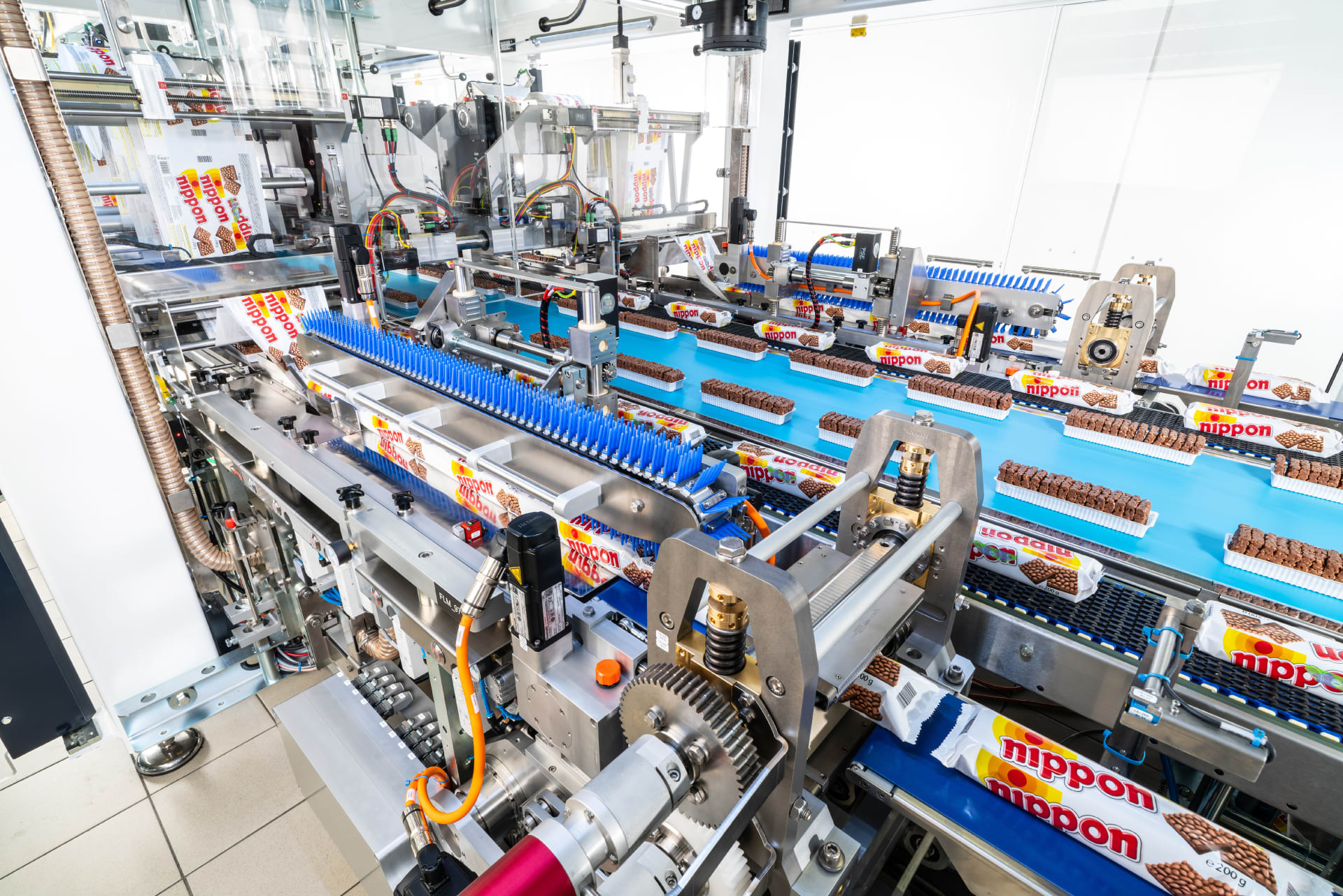
Durch das einzigartige Siegelsystem des Flowpackers bietet Schubert seinen Kunden beim Verpacken von Produkten in Schlauchbeutel eine besonders große Flexibilität.
Flexibles und schonendes Siegelsystem von Schubert
Das Heißsiegeln hat gegenüber der Kaltsiegelung also einige Vorteile. Der Trend zu nachhaltigeren Verpackungsmaterialien lässt sich allerdings auch mit der bisherigen Heißsiegeltechnologie schlecht umsetzen. Denn neu entwickelte Lösungen wie recycelbare Monofolien oder nachhaltige papierbasierte Folien sind anspruchsvoller bei der Siegelung. Hier sind flexiblere Technologien in der Schlauchbeutelmaschine gefragt, die sowohl herkömmliche Heißsiegelfolien als auch nachhaltigere Varianten verarbeiten können. Generell entsteht die Siegelnaht beim Heißsiegeln nicht nur durch Druck, sondern vor allem durch Wärmezufuhr an der Siegelstelle. Konventionelle Heißsiegelfolien sind Verbundmaterialien, die auf der Siegelseite durchgehend mit einer Siegelschicht versehen werden. Durch die Hitzeeinwirkung schmelzen die Siegelschichten der beiden Folienteile an der vorgesehenen Siegelnaht leicht an und verbinden sich.
Beim konventionellen Heißsiegeln erfolgt die Wärmezufuhr ähnlich einer Elektroherdplatte über erhitzte Siegelbacken oder Rollen und dringt mit bis zu 200 Grad Celsius von außen durch die Schlauchbeutelfolie bis an die Siegelschicht. Anders dagegen beim Ultraschall: Durch die Reibung, die mit Hilfe der schwingenden Sonotroden zwischen den Siegelflächen entsteht, wird die Schmelztemperatur genau dort erzeugt, wo sie benötigt wird. So können sich die Siegelschichten miteinander verbinden. Die Siegelwerkzeuge bleiben dabei nahezu kalt. Beim Ultraschall wird die Wärme also genau an der Klebestelle erzeugt, und muss im Gegensatz zum herkömmlichen Heißsiegeln nicht von außen durch die Folie bis zur Innenseite durchdringen. Das macht die Ultraschallsiegelung zu einem besonders schonenden Verfahren, das gerne für sensible Produkte aus dem Pharmabereich oder wärmeempfindliche Lebensmittel wie Schokolade eingesetzt wird. Im Vorteil ist die Siegelung mit Ultraschall auch bei dickeren Folien mit hoher Dichtigkeit, aber vor allem bei den neuen nachhaltigen Folientypen. Denn bei Monofolien weist die komplette Folie mehr oder weniger die gleiche Schmelztemperatur auf. Dadurch kann die Folie außen beschädigt werden, bevor die Temperatur innen an der Klebestelle angelangt ist. Bei Verbundfolien dagegen hat die Außenschicht in der Regel einen wesentlich höheren Schmelzpunkt. Auch papierbasierte Folien lassen sich besser mit Ultraschall als mit konventionellen Heißtechnologien siegeln, da die Hitzeisolierung des Papiers keine Rolle spielt und die äußeren Schichten weniger hitzebeständig sein müssen.
Wie lassen sich diese Technologien nun am besten nutzen, um beim Siegeln flexibler zu werden? Die Antwort darauf heißt Flowpacker. Mit seiner Schlauchbeutelmaschine bietet Schubert eine hochflexible Lösung, die sowohl herkömmliche als auch nachhaltige Folien verarbeiten kann. Dazu nutzt Schubert nicht nur die Ultraschalltechnologie, sondern wahlweise keramische Heizelemente für die Längssiegelung. Diese Heizelemente bestehen nicht aus einer kompletten Siegelbacke, sondern aus zahlreichen keramischen Einzelelementen oder Segmenten in der Größe 5 x 5 Millimeter. Diese heizen hochdynamisch auf und kühlen im Vergleich zu herkömmlichen Heizplatten um ein Vielfaches schneller wieder ab. Zudem lässt sich jedes Element einzeln ansteuern. Das macht die Hitzeeinwirkung beim Siegelvorgang sehr gut kontrollierbar, dosierbar und ähnlich schonend wie Ultraschall.
Das spezielle Siegelsystem im Flowpacker verbindet das schonende und flexible Siegeln mit den keramischen Heizelementen oder das Ultraschallsiegeln bei der Längssiegelung mit einer einzigartigen, roboterunterstützten Heißsiegeltechnologie bei der Quersiegelung. Die fliegende Quersiegeleinheit ist ein kleiner Roboter mit drei NC-Achsen und ermöglicht es, den Siegelvorgang in Temperatur und Dauer exakt zu programmieren und im Prozess stets konstant zu halten. Dadurch bleibt die Siegelzeit identisch, auch wenn sich die Kettengeschwindigkeit verändert. So lassen sich mit einer längeren Siegeldauer beispielsweise niedrigere Temperaturen verwenden. Das Siegelverfahren ist so schonend, dass im Flowpacker problemlos auch sensible Produkte und nachhaltige Schlauchbeutelfolien verarbeitet werden können. So bleiben Hersteller über Jahre hinweg im Markt flexibel und sind für die Trendwende hin zu nachhaltigen Verpackungslösungen bestens aufgestellt.
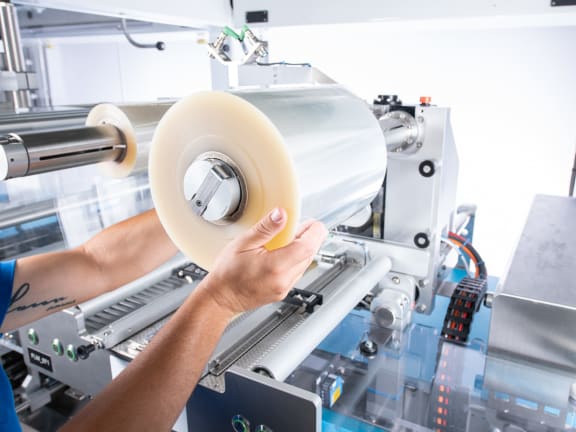
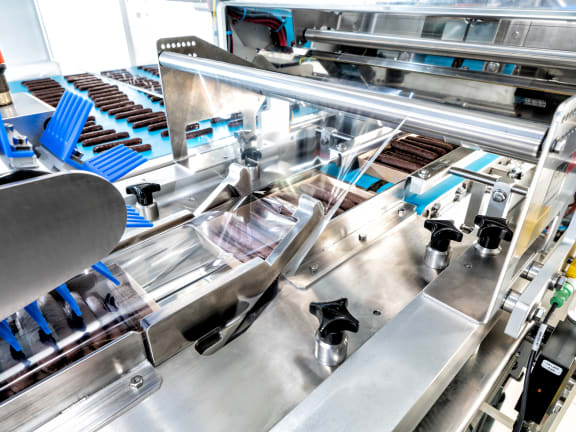
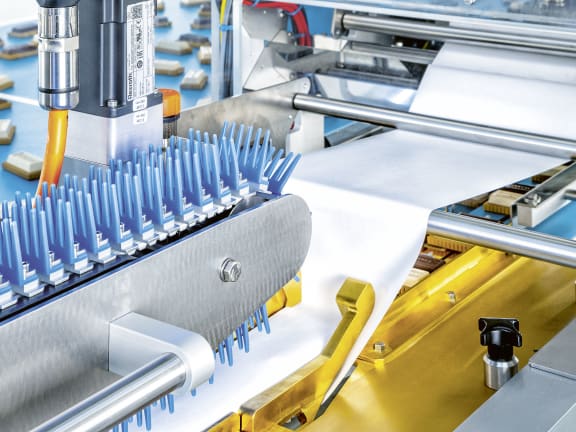